Tungsten carbide inserts welding fracture
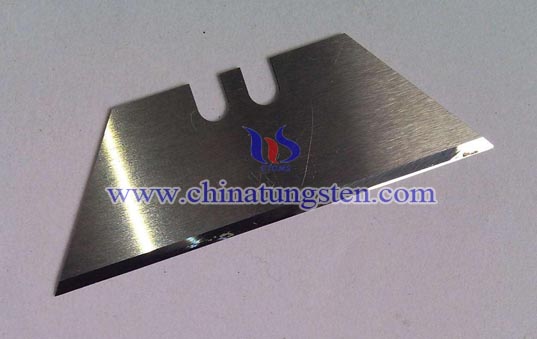
Welded tungsten carbide inserts have high hardness, wear resistance, heat resistance, high cutting performance, long life and other advantages, but prone to breakage during welding, the main reasons are:
1. tungsten carbide inserts at high frequency brazing easy to crack, due to the low coefficient of linear expansion of cemented carbide, cemented carbide linear expansion coefficient of only 4.5×10-6K-1, while the coefficient of linear expansion of steel approximately 15.5×10-6K-1, carbide alloy linear expansion coefficient is only 1/3 of that when brazing alloy tungsten carbide inserts and will produce very in part and carbide brazed joints inside At the same time, high carbide hardness, toughness is poor, high flexural strength, but the tensile strength is very low, so the tungsten carbide inserts is easy to crack.
2. Due to the thermal expansion coefficient of carbide inserts small, usually steel 1/2 ~ 1/3, when tungsten carbide inserts and blade steel welded, because it is not synchronized contraction in the formation of the weld zone is high internal stress, and in the cemented carbide inserts and more tensile stress, leading tungsten carbide inserts cracking. Welding stress is the main reason appears brazed tungsten carbide inserts cracks and joints of low stress fracture.
3. The high-frequency induction brazing too fast, easy to make the inserts or inserts overheating and melting the solder copper is not complete, so that the inserts are different hot and cold shrink, resulting inserts cracks.
4. Burnt tungsten carbide inserts, due to prolonged heating caused by manual welding blade, tungsten carbide inserts when heated to above 950 ℃, carbide surface begins to oxidize, a loose oxide layer. Accompanied by decarbonization phenomenon. When heated to 950 ℃ ~ 1100 ℃, the surface layer of oxidation occurs abruptly, the oxide film formed so brittle carbide, dramatically reducing the overall mechanical properties.
5. Brittle tungsten carbide inserts, after welding cooling too fast can cause uneven heat distribution, the blade surface transient tensile stress. Tensile stress greater the faster the cooling rate produced, their tensile strength over the blade, the blade will crack.
For these reason, we can reduce the high-frequency brazing temperature, preheat, slow cooling after welding, plus compensation for copper, ponds will increase blade capacity and improving the appropriate preventive measures, thus greatly improving the tungsten carbide inserts welding reliability and service life.