硬质合金刀片焊接断裂
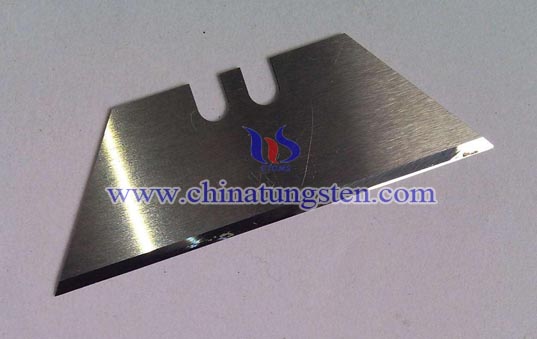
焊接式硬质合金刀片具有硬度高、耐磨性好、耐热性好、切削性能高、使用寿命长等优点,但其在焊接时易发生断裂情况,主要原因有:
1. 硬质合金刀片在高频钎焊时易产生裂纹,是由于硬质合金的线膨胀系数低,硬质合金线膨胀系数仅为4.5×10-6K-1,而合金钢的线膨胀系数约为15.5×10-6K-1,硬质合金线膨胀系数仅为合金钢的1/3,当硬质合金刀片与合金钢钎焊后,会在钎焊接头部分及硬质合金内部产生很大的内应力;同时,硬质合金的硬度很高、韧性差、抗弯强度高但抗拉强度都很低,因此硬质合金刀片容易开裂。
2. 由于硬质合金刀片的热膨胀系数较小,一般为合金钢的1/2~1/3,硬质合金刀片和合金钢刀体焊后,由于不能同步收缩,会在焊缝区形成很高的内应力,表现在硬质合金刀片上多为拉应力,导致硬质合金刀片开裂。焊接应力是钎焊硬质合金刀片时出现裂纹以及接头低应力断裂的主要原因。
3. 高频感应钎焊加热速度过快,易使刀体或刀片局部过热以及铜焊料熔化不完全,使得刀片和刀体冷热收缩不同,从而产生刀片裂纹。 4. 硬质合金刀片过烧,由于手工焊刀片时长时间加热而造成硬质合金刀片在加热至950℃以上时,硬质合金表面开始氧化,生成疏松的氧化物层。同时伴有脱碳现象。当加热至 950℃~1100 ℃时,表面层会发生急剧的氧化,形成的氧化膜使硬质合金变脆,综合力学性能大幅降低。5. 硬质合金刀片脆性大,焊后冷却速度过快会造成热量分布不均,使刀片表面产生瞬时拉应力。冷却速度越快产生的拉应力越大,超过刀片自身抗拉强度时,刀片就会出现裂纹。
针对硬质合金刀片产生断裂的原因,可采取降低高频钎焊温度、焊前预热、焊后缓冷、加补偿铜片、增加刀片容料池将相应的预防和改进措施,从而大大提高硬质合金刀片焊接的可靠性及使用寿命。