tungsten carbide inserts welding methods
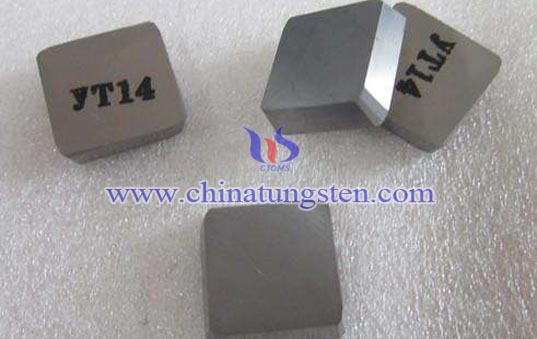
Welded tungsten carbide inserts have high hardness, wear resistance, heat resistance, high cutting performance, long life and other advantages. By arbor welded carbide blade, welding forming connected into one. And compared with overall mechanical clamping type tungsten carbide cutting tools, it has lower cost, this kind of tool in the machinery manufacturing industry has been widely used. And as one of the key components of cemented carbide inserts in the welding will crack, causing the blade scrapped, so pay attention to carbide blade welding methods is important.
Tungsten carbide inserts contains a lot of elements, there is a brittle, toughness poor shortcomings, the use of welding process forming hardened tissue and prone to cracking. When the residual stress is greater than the tensile strength of tungsten carbide, tungsten carbide inserts surface may crack. Therefore, the tungsten carbide inserts welding process must take effective measures, in order to obtain a satisfactory weld joints.
After brazing tungsten carbide inserts and inserts welding quenching methods and inserts welding process parameters is a major factor when tungsten carbide welding tool quality. tungsten carbide inserts at high frequency brazing prone Weld cracks thus affecting the quality and life of the tool. tungsten carbide and steel welding methods commonly used oxyacetylene flame brazing, vacuum brazing, arc welding, plasma arc welding, friction welding, electron beam welding, plasma arc welding and inert gas welding and so on. Oxyacetylene flame brazing equipment with its simple, versatile features, commonly used in small quantities for small and medium welding tungsten carbide cutting tools, through the use of reasonable methods and choose the correct heating process can weld high-quality hard alloy tool. Therefore, oxyacetylene flame brazing become one of the most commonly used method for brazing. tungsten carbide inserts welding selection oxyacetylene flame brazing with molten solder in good wettability and liquidity, after solidification greater ductility and toughness, while ensuring adequate use of inserts strength.