tungsten carbide inserts damage
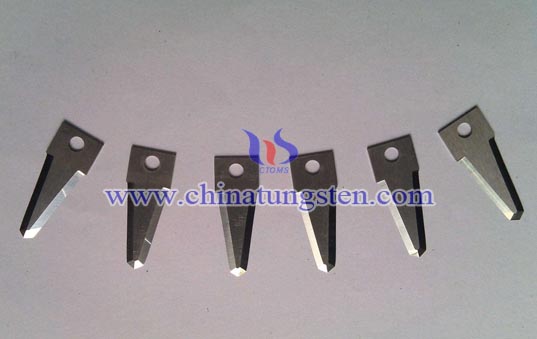
Tungsten carbide inserts cracks damage in the cutting process (especially in intermittent cutting) is a big processing problems. A correct understanding of the causes of cracks and take appropriate preventive measures are the key tool to improve working life and cutting performance of tungsten carbide inserts.
When tungsten carbide inserts performing intermittent cutting, its damage form as a continuous cutting, and can be divided after flank wear, cratering, knives permanent deformation and cutting edge mechanical breakdown. Once tungsten carbide inserts produces heat cracks, can easily lead to breakage occurs cutting edge chipping and flaking rake. During the cutting process, mechanical loading and thermal stress, while the presence of the tool, which may cause the tool compressive plastic strain. Such plastic deformation may occur in the tool-chip contact region the highest temperature portion, which portion is located within a certain range of the cutting edge on the back.
There are two forms of tungsten carbide inserts breakage: 1) cutting edge chipping; 2) between the rake face between two crack localized spalling. In the intermittent cutting process, the inserts chipping occurs reasons not yet clear, but it may not have relations with the thermal stress, because chipping phenomenon also occurs at low speed cutting. However, cracks in the cutting edge in the vertical direction may be generated by thermal stress related. For tungsten carbide inserts, when between two part of the strip when peeling cracks occur between the rake face, often directly caused by thermal cracking inserts breakage. Affected by the type of spacer used. Therefore, thermal stress generated by compression in the inserts process can be controlled by the volume of the inserts temperature. Before the start of the tungsten carbide inserts preheat treatment can reduce the high initial compressive stress, which will help improve the performance of the inserts.