tungsten carbide coated inserts
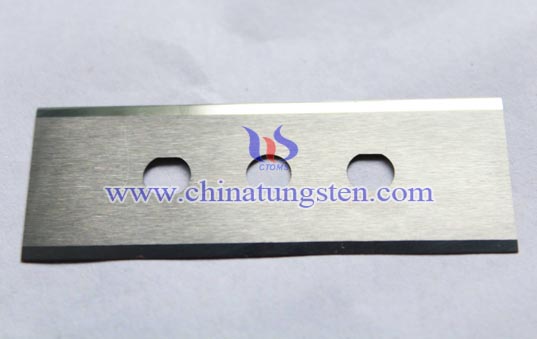
In modern industry, the application of high strength, high hardness, heat and other metal materials more widely, in order to adapt to the machining of new materials and high-performance tool material requirements, tungsten carbide coated inserts has a wear-resistant, high toughness, excellent chemical stability and good overall performance, which can effectively improve tool life and processing efficiency. Used in some advanced industrial countries produced using coated tungsten carbide indexable inserts has more than 50%.
Coating process is called on a material substrate coated with a hard compound to meet the different needs and purposes and tungsten carbide inserts coating on the cemented tungsten carbide substrate is coated with a thin layer of decent (about 5μm ~ 9μm) high hardness and abrasion resistance compounds TiC, TiN, so that the tungsten carbide insert both high surface hardness and high wear resistance, but also a tough matrix. For example, TiC coated inserts hardness of HV3200, TiN coated inserts hardness HV3223, while ordinary tungsten carbide inserts YT14 hardness about HV1500, YG8 tungsten carbide inserts for HV1200. Meanwhile, tungsten carbide coated inserts coating method, there are two categories: physical vapor deposition method that PVD and CVD method that is chemical vapor deposition.
Because tungsten carbide coated inserts has a higher hardness and a strong anti-adhesive, anti-scratch ability, and good chemical stability and oxidation resistance, these excellent overall performance will be effective against a variety of tools in the form of wear, inserts durability greatly improved, or the durability of the inserts at a certain allowable cutting speed, to increase productivity. tungsten carbide coated inserts cutting performance in improving the effect is significant, not only the cutting force and friction coefficient is reduced, thereby reducing power consumption, but also reduce the inserts wear, doubling the inserts durability, reducing the tool material consumption, thereby reducing the total cost. And at the same tool life, tungsten carbide coated inserts cutting speed can be increased, so that productivity can be improved.